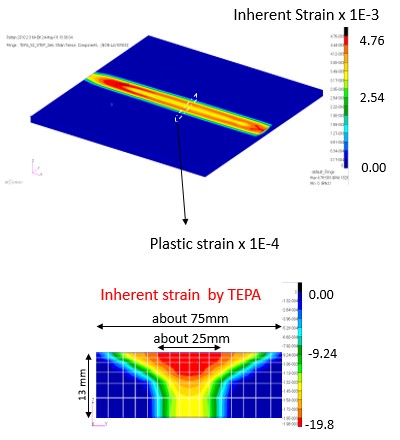
Fatigue Strength Analysis
- Fatigue strength analysis due to wave load
- Prediction of distortion
- High-Frequency Mechanical Impact (HFMI)
- Fatigue testing and experiments
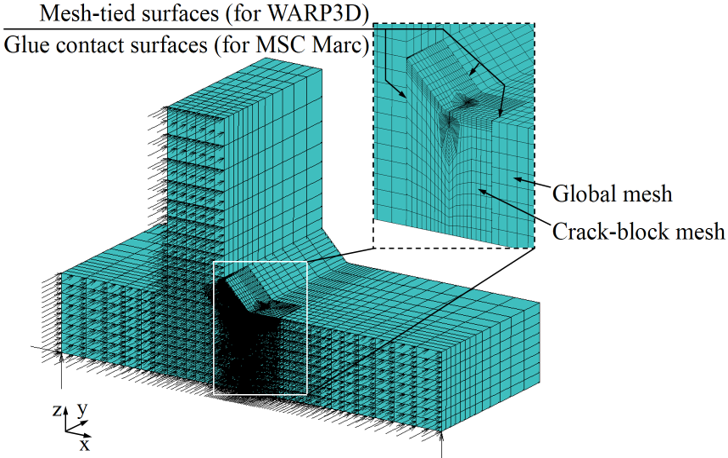
Fracture Mechanics analysis
- Evaluation of Stress Intensity Factor
- Estimation of fatigue crack propagation rate
Anti Corrosion Analysis
- Experiments
- Simulation
Welding analysis
- Experiments
- Simulation
Fatigue strength analysis for the ship structures
Statistical wave load model for fatigue strength analysis for the ship structures
As the wide use of high-tensile steel in ship construction and the trend of an increasing size of ship structures, ships become more flexible and more sensitive to wave loadings when they are crossing the oceans. The wave loading applied on ships will cause continuously changing structural stresses, which can result in fatigue problems in ship structures. Further, due to large uncertainties involved in ship fatigue design, fatigue cracks can be observed much earlier than expected. The presence of fatigue cracks greatly affects a ship’s serviceability. Hence it is of great interest to study a ship’s sailing capability after a fatigue crack is observed at a major component that undertakes the global strength. Instead of traditional high cycle fatigue assessment for ship structures, it is of great interest to employ fracture mechanics to predict the fatigue crack propagation.
Further, in recent years, is important to ships to comply with the Ship Energy Efficiency Management Plan recommended in the energy efficiency measures by International Maritime Organization, and operation based on weather routing has become imperative these days. Those ships never experience extremely severe seas. This will have a significant impact on extreme load and wave loading. Therefore, in order to study a ship’s sailing capability, e.g. before the crack reaches the critical length, it is an important task to know its future sailing environments. Based on the statistical wave load model, called “storm model”, that can emulate ocean wave sequences developed by Tomita et al. (1995) (the 1st generation, 1G model) and its refinement proposed by Kawabe (2002) and Osawa et al. (2006) (the 2nd generation, 2G model), Prasetyo et al. (2012) (the 3rd generation, 3G), research is conducted to consider the effect of the ship operation based on weather routing on the fatigue strength of the ship structure. The effectiveness of the proposed wave load model is demonstrated by comparing the changing nature and the statistical characteristics of simulated sea state histories with those of the source oceanographic data.
Consideration of the relative heading angles in the 4G-storm model Change in wave height every one hour in a Bishop Rock to Florida voyage (From January 18th, 2003) Example of generated significant wave height sequences based on storm profiles with different storm duration Idealized random wave loading model (Tomita et al. 1995)
Prediction of distortion produced in welded structures
Welding distortion is an unavoidable problem in welded steel structures, such as ships and offshore platforms. Distortion not only degrades the performance but also increases the building cost of structure, and it should be straightened. For ships and offshore structures, straightening is usually performed by line or spot heating which introduces additional inherent strain into the steel plate. In order to optimize the straightening process, it is necessary to predict the deformation due to straightening by numerical simulation. Murakawa et al. (Trans. JWRI, 39, 2, pp. 103-105, 2010) developed an inherent strain based welding simulation FE code JWRIAN. Coarse shell FE elements are used in JWRIAN analyses. However, it is not easy to perform straightening analysis by using JWRIAN because gas heating’s inherent strain distribution range is much smaller than element sizes which are suitable for welding simulation.
In this study, a JWRIAN’s subsystem which can calculate initial strain due to straightening heating is developed. The contribution of straightening strain to initial strain force is calculated by performing higher order (up to 30 x 30 points for 4 nodes element) Gauss-Legendre quadrature, while other quantities (such as stiffness matrix and external force vectors) are calculated by ordinary order (2 x 2 points for 4 nodes element) quadrature. This makes it possible to assess the contribution of narrowly confined inherent strain precisely and inhibit shear locking of shell element. Inherent strain distribution given to JWRIAN’s element is calculated by performing three-dimensional thermal elastic-plastic FE analysis with fine hexahedron brick elements.
FE model for Thermal Elastic Plastic analysis Gauss integration point arrangement for an element size of 50x50x13 Elastic Analysis Thermal elastic plastic analysis
High-Frequency Mechanical Impact (HFMI)
Many factors are known to influence the fatigue life of materials and welded structures, such as residual stress, material hardening/softening, and surface roughness. The advantages of removing the potential threats of unwanted tensile residual stresses and exploiting the beneficial compressive residual stresses created by mechanical post-weld treatments are already known in welding communities.
Weld improvement methods have been investigated in many test programs and have in most cases been found to give substantial increases in fatigue strength. However, there are large variations in the actual improvements achieved, and the results obtained by various methods are not always ranked in a consistent manner. One explanation for the observed variations is the lack of standardization of the optimum method of application, but variations in the material, type of loading, and type of test specimens may also have influenced the results. The effectiveness of the treatment also depends heavily on the skill of the operator.
A mechanical post-weld treatment such as HFMI has been found to exhibit a significant fatigue life enhancement of welded joints. The effectiveness of this mechanical impact treatment is mainly based on the combination of three effects: improvement of the local work hardening, introduction of compressive residual stress, and closing of notches at the weld toe. However, there is a concern that the introduced compressive residual stress might deteriorate due to residual stress relaxation under cyclic loading, and the HFMI treatment might lose its effectiveness. There is a need to develop a practical method to investigate the cyclic loading relaxation, as well as, several aspects of this treatment.
Example of FE mesh of the flat plate and HFMI tool Example of FE mesh of the gusset welded joint model and HFMI tool
Fatigue crack propagation analysis by Fracture Mechanics approach
Evaluation of fatigue crack propagation is considered essential in maintaining the structural integrity of ships and offshore structures which are subjected to cyclic loads. For reliable fatigue crack propagation assessment, precise estimation of stress intensity factors (SIF) is necessary. SIF can be calculated in many different ways: numerical methods such as finite element analysis (FEA), and analytical methods. SIF in complex cracked geometries is usually evaluated by FEA. On the other hand, a lot of man-hours are consumed to generate finite element (FE) models for various crack sizes and different crack angles. Efficient methodologies to calculate SIF without repetitive procedures for FE modeling are proposed and verified in our work.
Current researches are related to the evaluation of mixed-mode SIF (MM-SIF) which are required for the fatigue crack propagation assessment. The influence function method is employed to get accurate solutions of MM-SIF effectively. The interaction integral method considering the crack face traction (CFT) is also employed in the calculation of MM-SIF so that the SIF solutions becomes more reliable and accurate.
Further studies are utilizing the proposed efficient techniques and MM-SIF results in fatigue crack propagation (FCP) assessment of welded joints in ship structures. For analysis of FCP, extended finite element method (XFEM) which is a powerful tool for fatigue problems will also be employed, and CFT will also be integrated into the XFEM. More accurate and reliable FCP rates are expected to be evaluated using the mentioned methodologies.
FEA of uncracked flat plate model FEA of uncracked flat plate model Comparison of MM-SIFs with reference solutions Inclined-cracked flat plate FE model for fracture mechanics analysis